A general contractor is a construction management professional who oversees projects to ensure they’re completed properly. They’re also responsible for obtaining building permits and arranging city inspections.
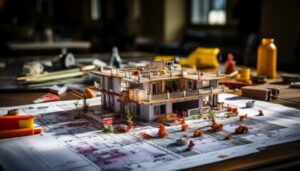
They’re a good choice for clients who want a single point of accountability and want to save money by preventing costly mistakes and negotiating cheaper prices on materials. Contact J&R Construction for professional help.
A GC’s first step in the construction process is creating an accurate cost estimate. This is an important component of their job, and it allows them to manage risk by ensuring the project stays on budget. This is especially critical if they are working under a fixed-price contract, where the contractor is responsible for any costs overruns.
Throughout the construction process, a GC may need to revise the budget in response to changes in scheduling or other factors. This is why choosing software with robust construction workflow integration is crucial. This feature synchronizes the budget with other financial documents and updates them automatically, reducing errors and boosting efficiency. KonstructIQ’s invoice management and budgeting tools are an example of this type of digital platform, enabling contractors to streamline payments and boost cash flow.
A GC will also use the project schedule to manage their subcontractor resources. This will help them keep track of critical path deadlines and ensure that the project adheres to the original schedule. It will also help them coordinate with other stakeholders, including clients and other GCs. This coordination helps avoid conflicts and minimizes misunderstandings, which can lead to costly delays.
Scheduling
The goal of scheduling is to match project work tasks with available resources and time ranges. This reduces production bottlenecks and delays, allowing the completion of project tasks as soon as possible. It also ensures that the project meets deadlines and budget constraints.
Many general contractors have experience with a wide variety of scheduling techniques and tools. This includes Gantt charts and scheduling software. These digital tools help general contractors manage their projects and keep track of critical dependencies.
Using the right construction scheduling software can make all the difference in a project’s success. This software helps simplify complex project timelines by allowing users to view and modify their schedules with a single click. It can even create what-if strategies for unforeseen hazards and challenges.
One of the key factors in a successful construction project is getting the proper permits. Whether it’s for home renovations or a commercial building, city inspections are essential to ensure that the project meets local regulations. This is especially important for commercial construction, where the right permit can save you a lot of headache and expense.
A good general contractor will understand the ins and outs of the permit process, helping you avoid any delays or fines. In addition, they will be transparent about the process and provide a clear timeline for permit approval. This will help ensure that your project is completed on time and in compliance with local laws.
Design
During construction, the general contractor is responsible for the physical build. The GC is in charge of creating the vision and then ensuring that it actualizes in your space, within budget and correctly. Unlike architects and interior designers, who specialize in specific steps of the process, the GC is skilled at managing every aspect of your project from start to finish.
A GC will collaborate with the architect and design team to ensure that your plans are compatible with your goals and local building codes. The GC is also in charge of hiring subcontractors and scheduling them to complete the work. For example, the GC will schedule electricians to complete electrical wiring before drywallers arrive, and he or she will verify that the subcontractors are meeting all requirements set out in the contract.
When the GC participates in the design phase, he or she can use value engineering principles to help you establish a realistic budget. The GC can also anticipate potential bottlenecks and provide solutions before they occur. This can save you money and avoid costly delays.
The GC can also manage the building process by collaborating with the owner and design team on changes to the original plan. They are also skilled in resolving problems during construction. This can include unforeseen challenges, such as unfavorable weather or delays in delivery of materials. The GC can solve these issues by using their problem-solving skills and finding creative solutions.
Permits
As the linchpin of construction projects, GCs maintain clear communication and coordination with clients, architects, designers, and specialty contractors (also known as subcontractors). They also act as the primary point of contact to keep everyone on the same page. This involves facilitating meetings, providing updates, and answering any questions or concerns.
The general contractor oversees the project by ensuring that all work is up to code and in compliance with the client’s vision. They may also handle the permitting process, if necessary. They typically use a permit management tool that securely stores all required documents and reminds subcontractors of expiration dates.
General contractors are also responsible for handling financial aspects of the project, including budgets and invoices. They are also capable of negotiating contracts and handling change orders. GCs manage residential and commercial construction projects, from remodeling homes to building skyscrapers.
As a licensed contractor, they are held to high professional and ethical standards. This means that they must maintain current licenses and attend continuing education classes to stay on top of industry trends and new construction technologies. They must also adhere to a code of ethics and abide by all local regulations. Moreover, GCs must be able to accurately communicate regulatory requirements to the public. If they fail to comply with these standards, they could face serious legal and financial consequences. This includes potential fines, lawsuits, or even license revocation.
Subcontractors
Subcontractors are specialists in their field who perform tasks that aren’t within the scope of a general contractor’s skill set. This includes jobs like plumbing, electrical work, and HVAC installation. A GC works closely with these specialists to ensure that tasks are scheduled in coordination and that labor is efficiently managed.
The best construction subcontractors are able to estimate materials costs, labor hours, and project scope with accuracy. They also track construction progress and document milestones. This transparency allows them to effectively collaborate with GCs and safeguard their profit margins on each project. Subs also have a responsibility to enforce construction safety protocols, from personal protective equipment to fall protection.
While subcontractors don’t work directly for a GC, they are responsible to their clients for their performance and the quality of their work. A GC’s role is to act as the linchpin between owners, designers, and specialty contractors. GCs are often held liable for project delays and cost overruns, site safety compliance, and workmanship issues.
GCs communicate extensively with clients, especially on more expansive project matters and as the construction process evolves. While they may delegate granular tasks to general laborers, they typically retain decision-making authority and consult with clients on significant matters.
Quality Control
Large-scale construction projects often involve multiple subcontractors, each with specialized skills and expertise. To ensure the project stays within budget and on schedule, the general contractor manages subcontractors, overseeing their daily operations and ensuring all work meets quality standards and design specs. They also handle problem-solving and miscommunication issues that may arise during the project, resulting in inefficiencies and additional expenses.
In addition to hiring subcontractors, the general contractor selects and negotiates prices for materials and supplies. They also use tools like CoConstruct to track costs and monitor expenditures. During the construction process, they conduct regular inspections to ensure that the project progresses smoothly and according to plan. They are the main point of contact for the client, providing updates and discussing any changes.
Another critical part of the job is ensuring safety. They implement strict safety protocols and provide ongoing training to employees on site. This is particularly important during new constructions where workers are unfamiliar with the environment. They also regularly inspect and monitor the construction site to prevent accidents and ensure compliance with Occupational Safety and Health Administration regulations. When the project is completed, they perform a final walk-through with the client and provide all necessary documentation including warranties, operation manuals, and lien waivers. This ensures a smooth transition and a successful project outcome for the client. Managing subcontractors can be challenging, especially when it comes to payment. They need to have enough funding to purchase the materials they need and to pay their employees. To avoid problems, the GC will typically negotiate upfront contracts and establish a payment schedule.